Troubleshooting Common Letterpress Printing Problems
Letterpress printing, a beautiful and tactile craft, can be incredibly rewarding. However, even experienced printers encounter challenges. This guide addresses common letterpress printing problems, from uneven ink distribution to registration issues, and offers practical solutions to get your prints looking their best. Understanding the intricacies of letterpress also requires an appreciation for its history and design principles; for those interested in the broader context, you might find a journey into a brief history of letterpress insightful.
1. Uneven Ink Distribution – The Ink’s Not Coating Evenly
One of the most frequent issues is uneven ink coverage. This can manifest as darker areas in some parts of the print and lighter areas in others. Several factors contribute to this:
- Ink Viscosity: The ink might be too thick or too thin. Experiment with adding a small amount of ink thinner or a touch more ink to your ink plate. Always mix thoroughly. The right consistency is crucial, and for more in-depth advice on achieving the ideal color and tone, be sure to explore ink and color mixing for letterpress.
- Pressure Inconsistency: Uneven pressure across the printing surface leads to varying ink transfer. Ensure your press is properly calibrated and the pressure is consistent. Check your packing material (packing tape or chasers) for irregularities.
- Ink Plate Condition: A damaged or uneven ink plate will not distribute ink evenly. Examine the plate carefully for scratches or wear.
- Paper Properties: The type of paper you're using affects ink absorption. Absorbent papers require more ink, while coated papers may need less.
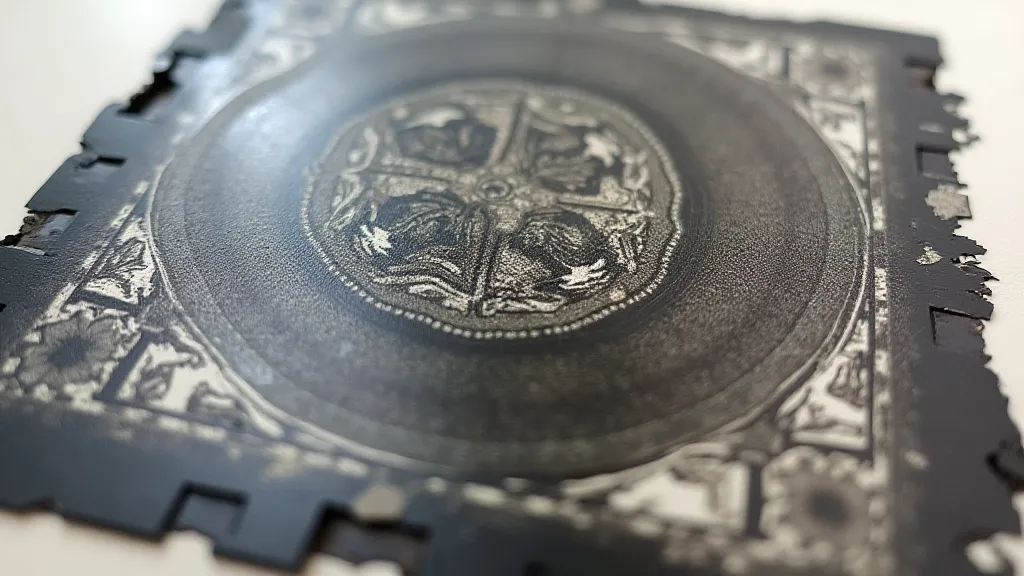
2. Registration Issues – Not Lining Up Correctly
When printing multiple colors or elements, accurate registration – the alignment of each printed layer – is crucial. Misregistration results in blurry or offset images. This is where a keen eye for detail and understanding of design principles become vital, and the harmony of letterpress and typography is a beautiful example of that synergy.
- Movement During Printing: The paper might shift slightly during the printing process. Secure your paper firmly on the chase.
- Improper Locking of the Press: The press’s locking mechanisms might not be completely secure. Double-check all locks after setting up each color.
- Differences in Plate Thickness: Even slight variations in plate thickness can throw off registration.
3. Impression Problems – Too Deep, Too Shallow, or Uneven
The “impression” is the characteristic debossed appearance of letterpress. Getting the right impression takes practice. It's a defining feature of the craft, contributing significantly to the tactile quality and visual appeal of the finished product.
- Impression Too Shallow: This results in a barely noticeable impression. Increase the pressure slightly.
- Impression Too Deep: This can crush the paper and create a harsh look. Decrease the pressure.
- Uneven Impression: This often indicates inconsistent pressure or variations in the printing surface.
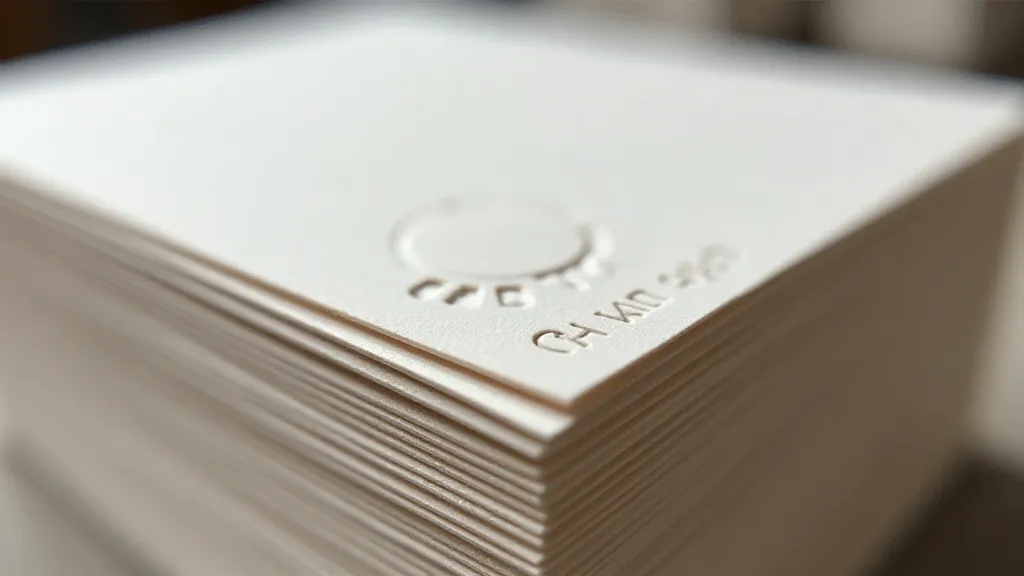
4. Paper Tears or Folds
Paper tearing or folding during printing is a frustrating problem. It usually stems from the paper's characteristics or the printing process itself. Selecting the right paper stock is paramount to a successful print run; it’s more than just about aesthetics; it’s about structural integrity.
- Paper Too Thin: Thin papers are more susceptible to tearing, especially with heavier impressions.
- Packing Issues: Packing material that’s too hard or uneven can damage the paper.
- Chase Too Tight: A chase that’s too tight restricts the paper's movement and can cause tears.
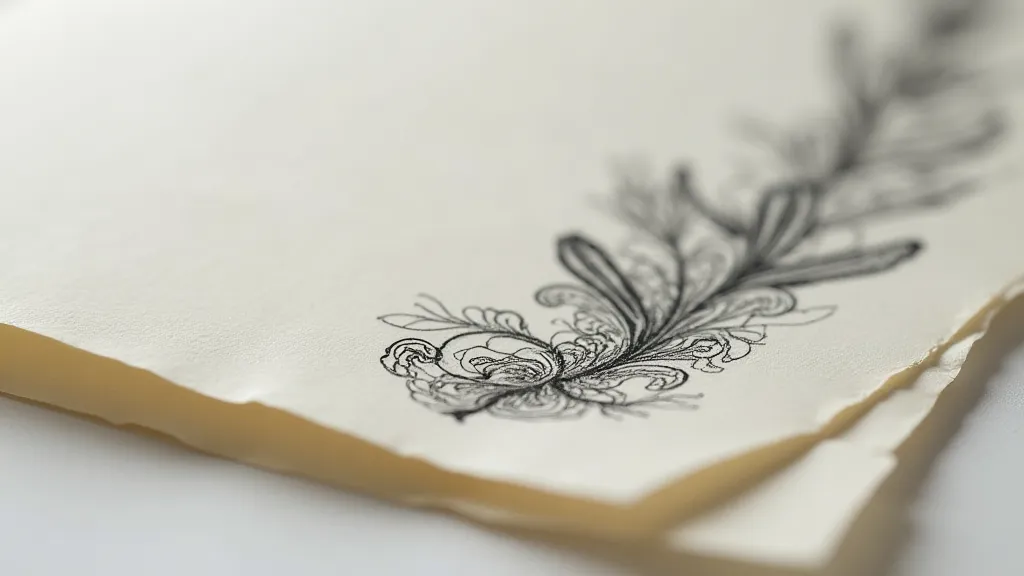
5. Ink Drying Too Quickly
Rapid ink drying can cause unevenness and create a tacky surface. This issue is often exacerbated by environmental conditions and can significantly impact the quality of your print.
- Dry Environment: Low humidity can accelerate ink drying.
- Ink Formulation: Some inks dry faster than others.
Letterpress printing is a demanding craft, but the rewards of producing beautiful, tactile prints are worth the effort. Don’t be discouraged by problems – each challenge is an opportunity to learn and refine your skills. With careful observation, diligent experimentation, and a little patience, you'll be printing like a pro in no time! The journey from beginner to skilled printer is paved with both technical understanding and creative exploration. Remember that even the simplest projects can offer valuable insights into the intricacies of the process.